(株)麗光
京都市右京区西京極豆田町19番地
TEL:075-311-4101
https://www.reiko.co.jp/
世界のエネルギー問題に
挑む新技術。
その太陽電池は驚くほど軽かった。手で簡単に曲げられるほど薄いシート状になっており、日陰はおろか室内でも発電可能。ビルの壁や窓といった垂直面や、光透過性が求められる場所、農業用ビニールハウスのような耐荷重性が低い場所など、これまでの太陽光パネルの設置が難しかった場所にも導入が期待されている。
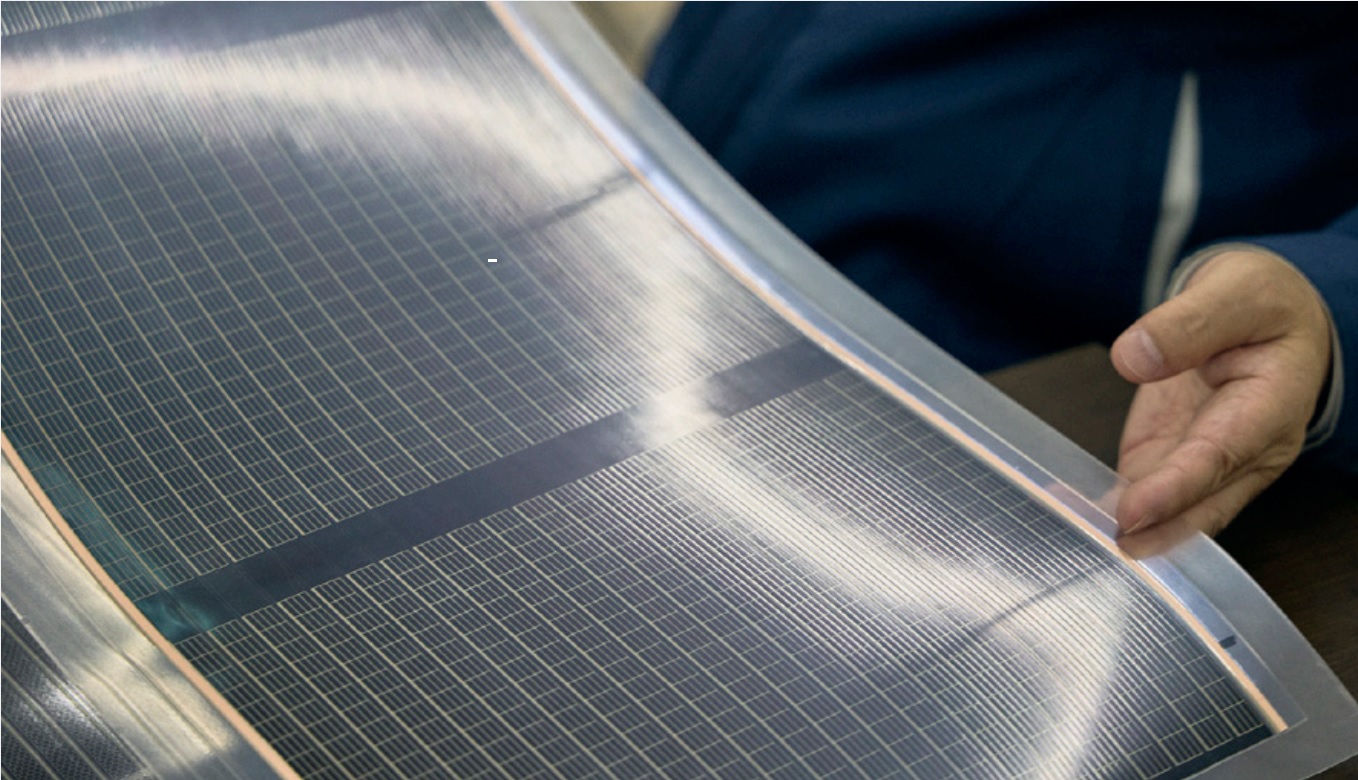
有機薄膜太陽電池のサンプル。会議室の蛍光灯の光でも発電、ライトが点滅する。
OPV(有機薄膜太陽電池)と呼ばれるその太陽電池の開発を進めているのが、京都に本社を構える高機能フィルムメーカー(株)麗光。来年70周年を迎える老舗企業は現在、実用化に向けた実証実験を進めている。世界のエネルギー問題の解決につながるかもしれない未来志向の新技術は、一体どのようにして生まれたのだろうか。
京都の伝統産業を支えた創業期。
「もともと麗光は、西陣織に使われる金銀糸の製造加工からスタートしました。法人の設立は1955年、私の生まれ年と同じです」。案内してくれたのは、麗光のフィルム事業を統括する小谷常務。新卒入社以降、この道一筋。製造から開発、さらには営業まで、フィルム事業の川上から川下まであらゆる経験を積んできた大ベテランだ。
伝統産業の一翼を担っていた京都の老舗が、最高クラスのクリーンルームを備えた先端企業へと変貌を遂げるきっかけとなった出来事がある。金銀糸の製造をより効率化するために、アメリカ製の真空蒸着機を導入したことだ。それまでは、薄い金箔を漆を接着剤に紙に貼り付け、それを細く切ったものをよじって糸を生産していた。だが、真空蒸着機を使えば成膜速度は圧倒的に速くなる。1959年、他社に先駆けて真空蒸着機を導入した結果、金銀糸の生産量が急増。事業成長は一気に加速した。
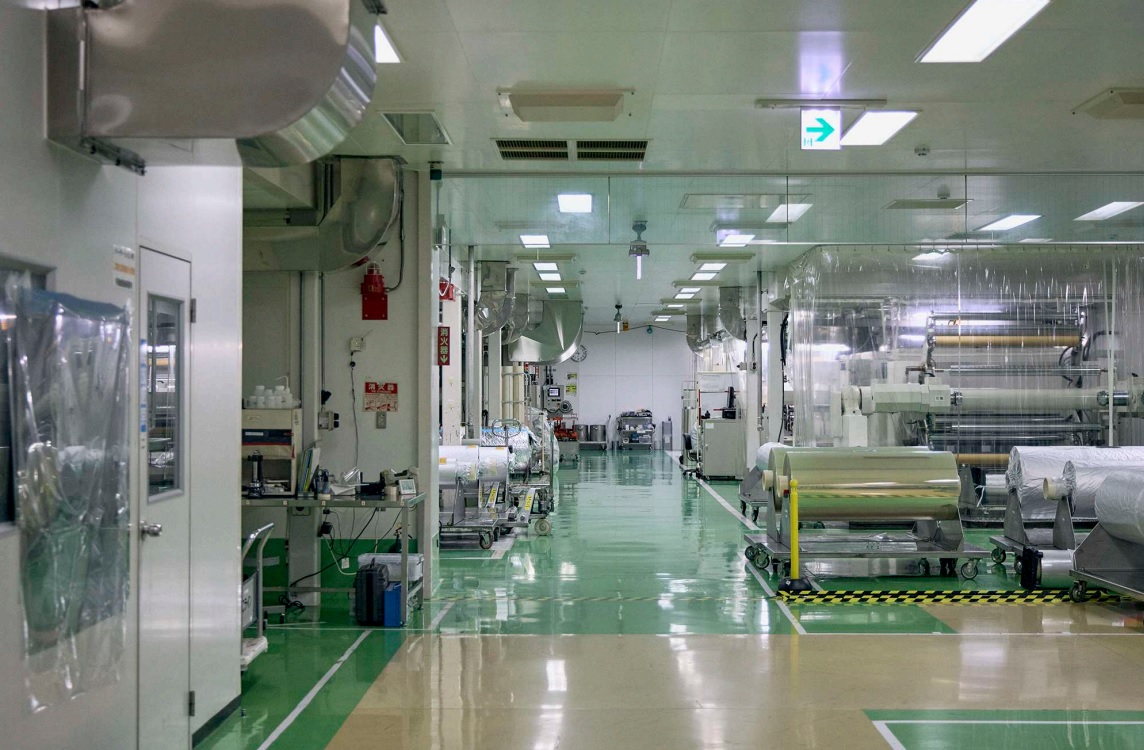
きれいなだけではなく、工場の規模に対して圧倒的に人が少ない。生産性の高さがまざまざと感じられた。
「それでも、次第に繊維業界からの需要も少なくなってきたんです。また、伝統産業だけに特化した事業では成長にも限界がある。1960年代に入ってからは、繊維事業で培った自前の技術を他の用途に活かせないかと多方面にアンテナを張り、新たな成長の道を模索しはじめました。世の中から常に最新のニーズの種を見つけ、分野を問わず製品化に向けてチャレンジする。そうした麗光独自の企業文化は、その当時から育まれていたのかもしれません」
湿気と酸化から、
スナック菓子を守れ。
「若い人はご存じないかもしれませんが、私たちが製品化する以前は、スナック菓子のパッケージは透明のフィルムで中身を見せるのが主流でした。でも、透明フィルムはバリア性が低く外気や光を透過させてしまう。結果的に、油が酸化しやすかったり、すぐに湿気てしまうという課題に直面していた。それを解決したのが、アルミ蒸着によるガスバリア技術です」。
麗光は、1968年にはガスバリア技術を確立し、繊維事業の枠を飛び越え包装材事業へと参入していた。当初はアイスクリームなど冷菓のパッケージとして重宝されていたと言う。麗光の包装材事業が大きく飛躍したのは、1983年のこと。透明フィルムが常識とされていたスナック菓子業界に、バリア性の高いアルミ蒸着フィルムを日本で初めて提案したことがきっかけだった。業界最大手のお菓子メーカーに採用され、以来アルミ蒸着フィルムを使ったパッケージは、業界のスタンダードとなっていく。
その後も、繊維分野や包装材分野だけでなく、薄膜加工というコア技術を武器に様々な市場に挑みつづけた。1990年代には液晶ゲーム機に麗光のフィルムが採用された。また、スマホ以前に世界中で使われていた携帯電話(フィーチャーフォン)の製造にあたっては、液晶裏の反射フィルムに麗光の製品が図面指定され、世界中へと広がっていくこととなる。実は、その反射フィルムに使われていたのが、『銀』。創業時、金銀糸を製造していた際のノウハウが、数十年を経て、麗光に新しい未来を連れてきたのである。
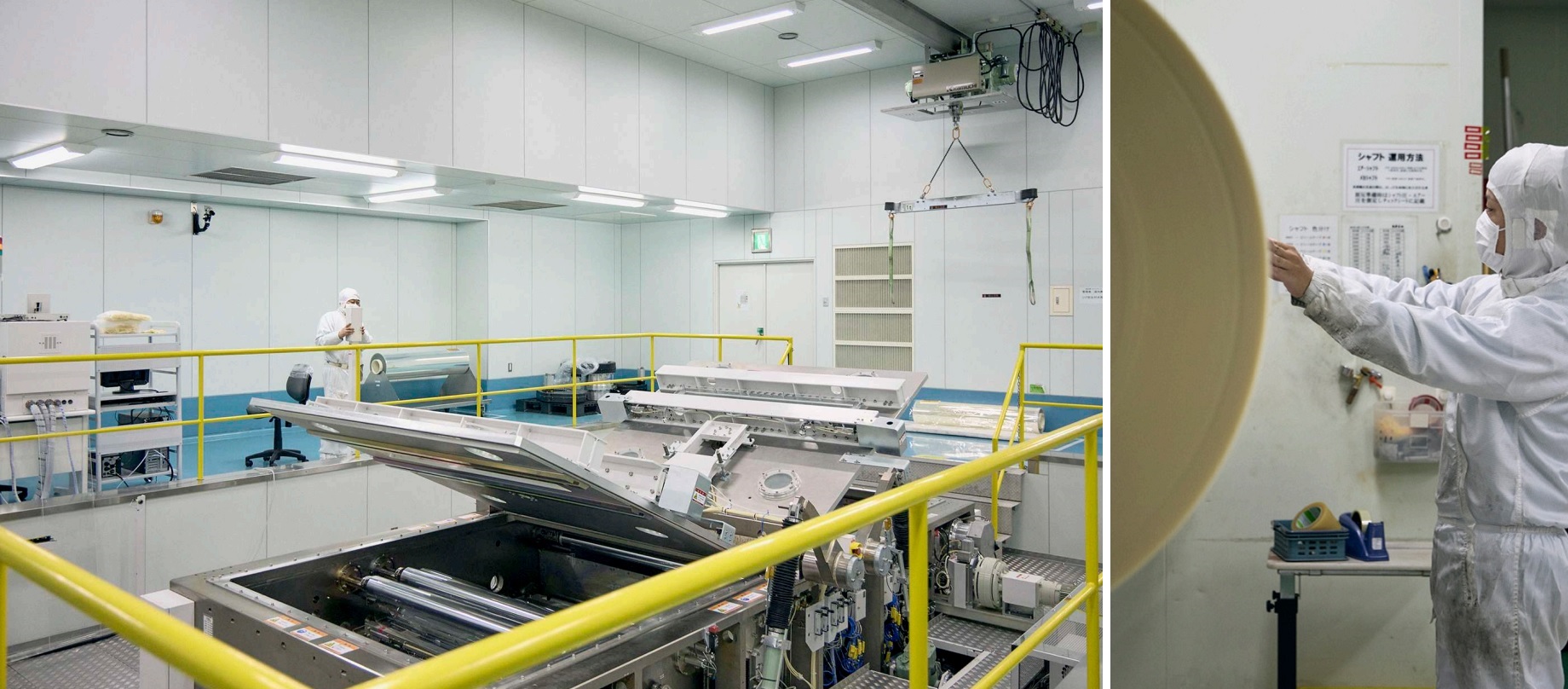
[写真:左]多様なフィルムを生産する麗光では、工場に置かれる機械の種類も多種多様。[右]フィルムひと巻あたりのボリュームは、長いものだと5万メートルを超える。いかに歩留まり率を上げるか、そこに技術者としての知恵や技術が問われる。
市場に求められてから
動くのでは、遅すぎる。
「様々な市場ニーズに応えることで、私たちは成長してきました。しかし、ニーズに応えようと思ったら、求められてから動き出すのでは遅すぎる。業界動向や展望を先読みし、少し先の未来に求められそうな技術や製品を、ニーズに先駆けて開発しておく。『こういうものできる?』というお客様の相談に『できます!』と即答し、最短で試作をお持ちする。そうした努力が認められた結果として、様々な製品に当社のフィルムを採用していただけました。お声がけいただいてから開発しているようでは、ニーズに応えることはできませんから」。
顧客要望はますます厳しくなり、今ではほんの少しのコートのムラや極めて小さな異物の混入も許されなくなってきている。今後、その傾向はさらに加速していくだろう。麗光では、そうした将来を見据えて最高レベルのクリーン環境を用意した。バリア性に関しても市場からのニーズが届く前に、実現可能な最高レベルを追求することを決意。数億規模の投資をし、試行錯誤を繰り返した。紆余曲折を経て誕生したのが、『10-5g以下/㎡・day(1日でフィルム1平米を通過する水蒸気量が10のマイナス5乗グラム以下)』という他を圧倒するバリア性。有機ELディスプレイでも使用できるレベルの超高機能フィルムが完成した。結果、有機ELディスプレイに使われることはなかったが、電子ペーパー用のバリアフィルムや海外の小売店で活用が進む電子棚札に採用され、世界中へと広がっている。
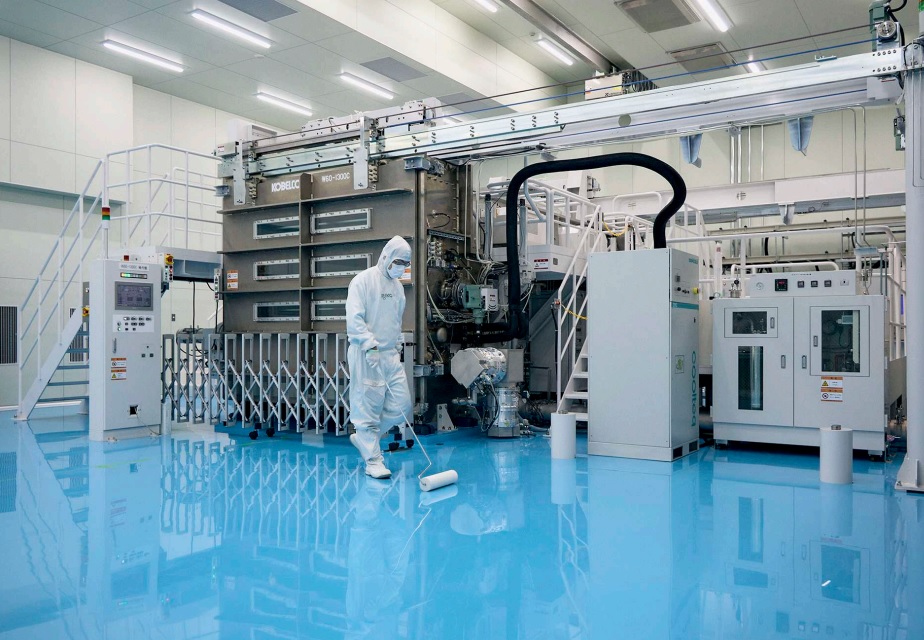
工場の床に反射するのは、まるでウユニ塩湖のような鏡面世界。『10-5g以下/㎡・day』という超ハイバリアフィルムはここから生まれる。
常に挑戦する姿勢が、
偶然を必然に変えていく。
「最初に紹介したOPV(有機薄膜太陽電池)は、実は自分たちが起点となって開発をスタートしたわけではないんです。大学の研究室に、当社の薄膜が研究に使えないかと持ち込んだのがきっかけでした。研究室で評価してもらったところ、『確かに良さそうだ』と好感触を得た。そこからさらに話が盛り上がり、『そういえば麗光さんは、太陽電池に欠かせない封止材も作れるし、薄膜加工の技術もあるし、十分な設備も持っている。全部組み合わせたらゼロからOPVを作れるのでは?』という話になったんです。うちでOPVを開発することになったのは、そうした色んな偶然が重なり合った結果なんですよ」。
小谷常務はそう謙遜するが、果たして本当に偶然の産物だろうか。常に新しいものを模索する社員の気質。「やってみたい」という社員の想いを後押しする企業風土。市場ニーズが顕在化していなくても、未来を読んでチャレンジする営業マンや技術者の先見性とその度量。世界最先端の太陽電池開発プロジェクトに白羽の矢が立ったのは、会社の草創期から育まれた、企業文化や独自技術が引き寄せた必然だと言えるだろう。
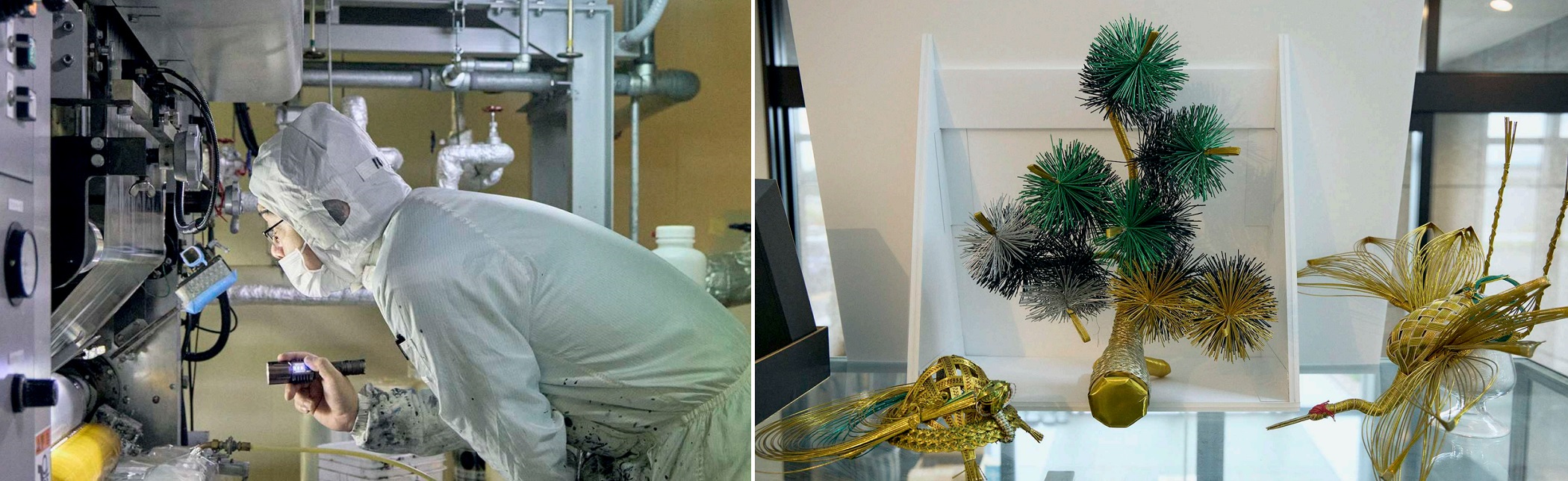
[写真:左]どうすれば目指す理想の品質を形にできるのか。アイデアを考え、試し、検討し、再度チャレンジする。AIにはできない。人間ならではの力が試される瞬間だ。[右]工場の玄関にある事業紹介のボード裏には、麗光の原点でもある「金銀糸」で作られた鶴亀松が飾られていた(祀られていた?)。長い歴史を超えて今も会社の土台を支えている。
「うちの会社も私も、来年には70歳を迎えます。老舗だ、ベテランだと言われますが、まだまだやるべきことはたくさんある。OPVを市場に広げていくための課題も山積みです。でも、私はたくさんの課題が立ちはだかるからこそ、仕事は楽しいと思うタイプ。『こんなことがやりたい』『こうすれば実現できるのでは?』と考えること自体が楽しいし、試行錯誤しながら、課題を一つ一つクリアしていく達成感こそが、仕事の何よりの醍醐味だと思うんです。若い人たちも、与えられた仕事だけじゃなくて『こんなチャレンジをしてみたい』という想いをどんどん発信してきてほしいですね」。
創業期の金銀糸の製造に始まり、包装材、高機能フィルムと長い歴史の中で挑戦の舞台を広げてきた麗光。その原動力となったのは、小谷常務の言葉にもある通り、難しい課題にも楽しみながら立ち向かっていく社員一人ひとりの強い想いだ。創業70年を超えても変わりつづける老舗企業は、5年後、10年後どんな技術で世界を驚かせてくれるのか。未来を正確に予想することはできないが、今とはまったく違ったチャレンジに挑んでいることだけは、きっと間違いない。
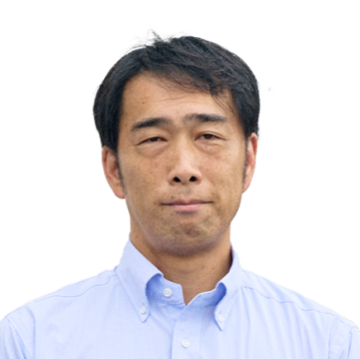
編集担当:碓井 和幸
チリひとつない大きなクリーンルームは圧巻!
今回初めて、電子ペーパーや太陽電池用のハイバリアフィルムを製造する日野工場にお邪魔させていただきました。なかでも、クリーン度クラス100のコーターを整備したクリーンルームは圧巻。先端研究施設のような工場では、未来型のモノづくりが行われていました。